Crafting a regenerative tomorrow: responsible materials in construction
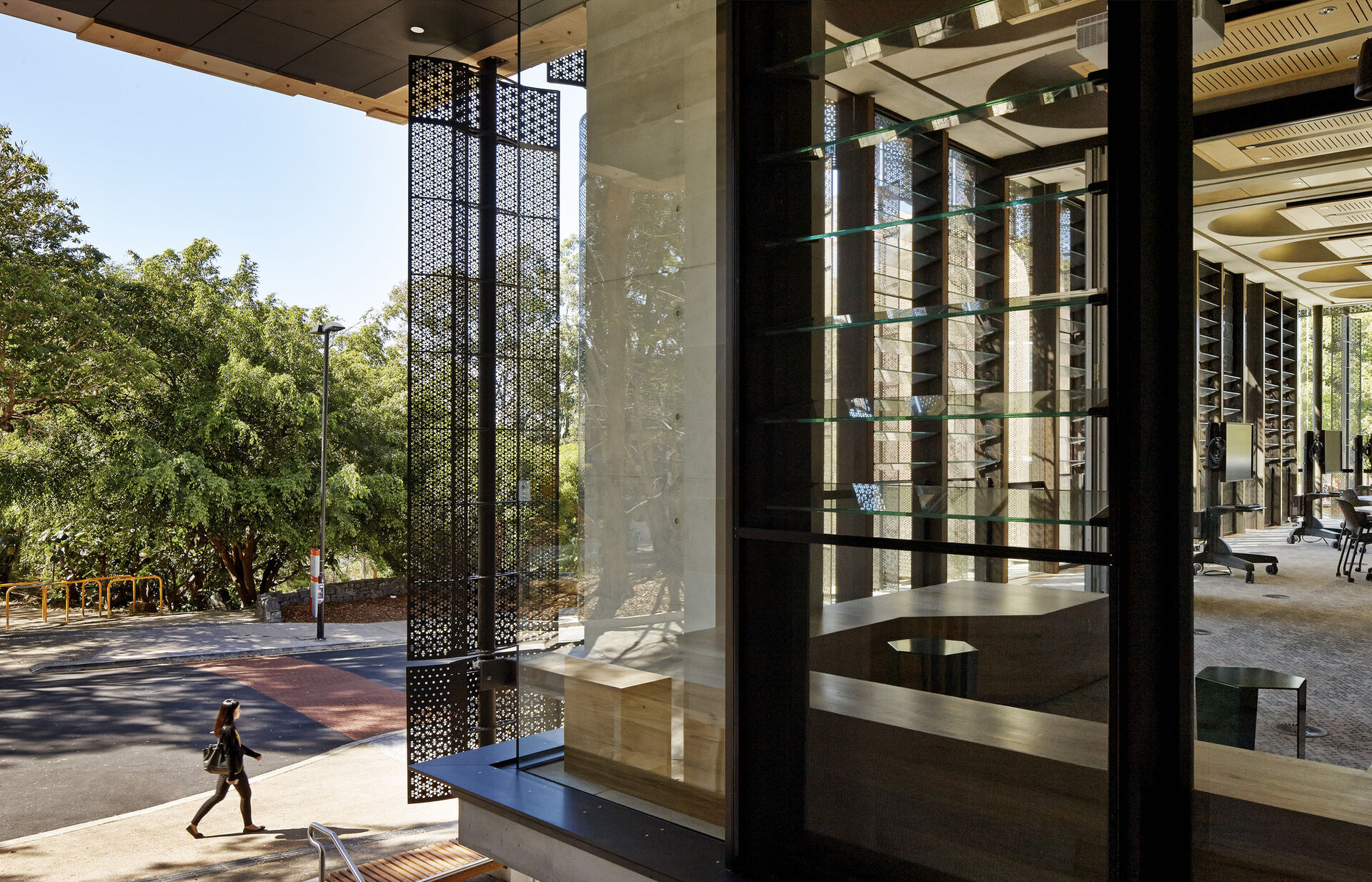
Author
Prioritising positive-impact materials is now imperative in the construction sector to reduce the industry’s effect on the environment. Associate Adam Paikos-Coe shares vital steps toward a more regenerative future.
Selecting and assessing products for any project is increasingly complicated due to data disparities and supplier transparency issues. Independent verification and understanding of a product’s components and production methods is crucial to confirm environmental claims and counteract greenwashing.
Adding to the challenges, the environmental impact of a product can fluctuate based on location, project type and scale, which means each situation requires tailored assessments. And some low-carbon products, such as Orientated Strand Board, typically made from waste products, can deteriorate rapidly and is difficult to recycle, meaning it could show a larger carbon footprint than products with higher embodied carbon but extended lifespans.
“Buildings are currently responsible for 39% of global energy related carbon emissions: 28% from operational emissions, from energy needed to heat, cool and power them, and the remaining 11% from materials and construction.”
— World Green Building Council
So how do you navigate the complex process of responsible material selection? Early identification of key stakeholders and knowledge transfer strategies are crucial in the lifecycle of a fit-out. Collaborating with suppliers offering product stewardship programs — a key demonstration of their dedication to product quality — can positively influence the supply chain. And comprehending material and product composition is essential not only for initial use but also for long-term durability and potential repurposing.
A prime example of repurposing materials is a new initiative called Resi Loop launched by The Australian Resilient Flooring Association (ARFA) to address waste management. This industry-wide program unites suppliers to recognise the importance of reusing materials for resilient flooring. This is a comprehensive industry scheme, and a pilot program has been established to collect construction waste and rejuvenate it into new products.
ENGAGING WITH A NON-VIRGIN MATERIAL SUPPLY CHAIN
Improving supply chain transparency is key to understanding a product’s lifecycle, from production to the potential for regeneration. Prioritising responsible material selection and integrating disassembly principles early in a project enables easier maintenance, refurbishment, and future adaptation, which reduces the likelihood of products ending up in landfills.
The Circle House project in Denmark aims to be the world’s first social housing project constructed according to circular economy principles. With 60 partners spanning the building value chain, the project focuses on demountable materials and minimal loss of value.
“The Circle House objective is that 90 per cent of materials can be demounted and reused or resold without loss of value — so-called ‘design for disassembly’.”
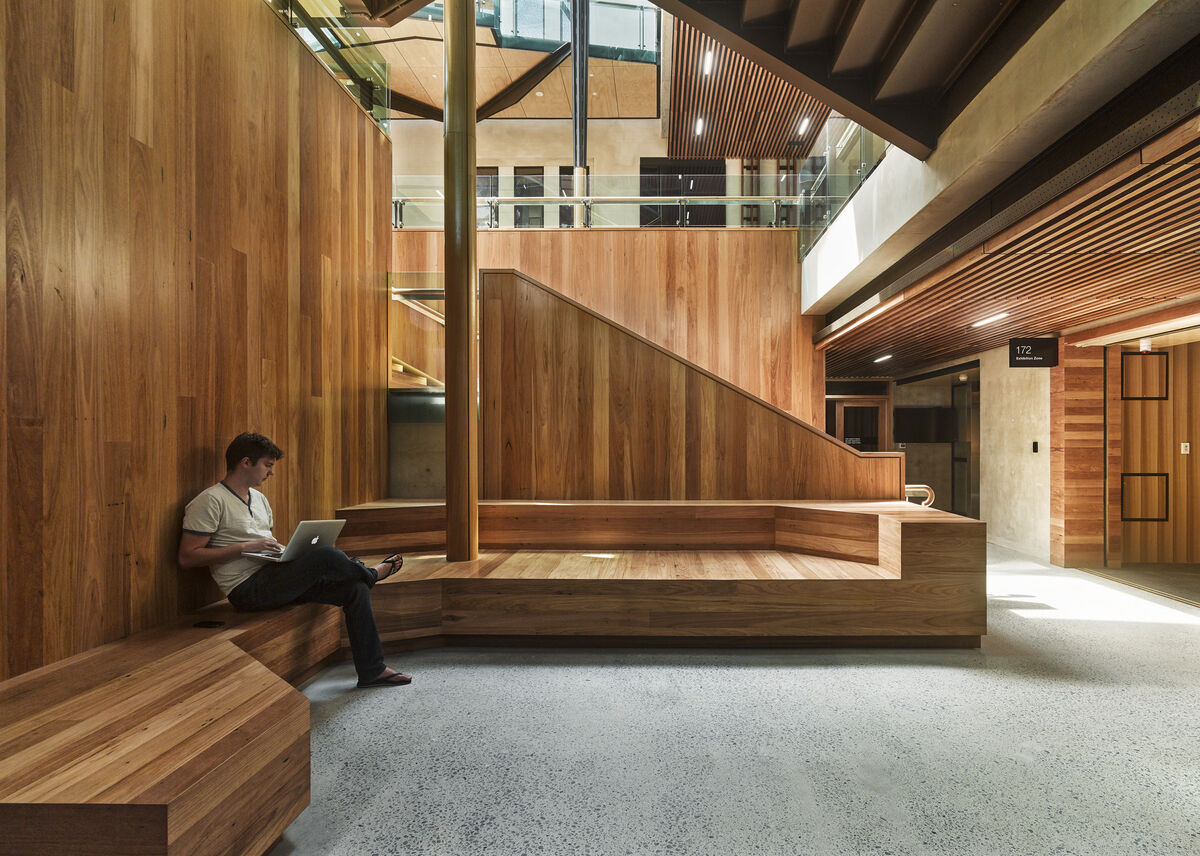
SOURCING SUSTAINABLE MATERIAL
Assessing supplier governance, manufacturing practices and modern slavery due diligence is now a crucial aspect of procurement and supplier agreements. This ensures truly sustainable products and fair treatment of those involved in their production.
The Green Building Council of Australia (GBCA) has introduced a Beta version of the Responsible Products Database and Calculator in its Responsible Products Program, which aims to lead the industry toward a positive legacy for current and future generations. Both the database and calculator will be integrated into the Green Star Building program and recognise 16 certification initiatives including Global Green Tag, International Living Future Institute and Cradle to Cradle. It currently features over 6,000 products and 800 manufacturers, with an expectation for continued growth.
The calculator tools are categorised into Structure, Envelope, Systems, and Finishes, and assist in streamlining the assessment of material choices from a project’s inception.
TOWARDS A REGENERATIVE FUTURE
Unlike its European counterparts, the Australian construction industry still has a long way to go when it comes to regenerative thinking and practice. Legislation is evolving to mandate whole-life carbon assessments and circularity statements as the industry does in the UK, and the carbon footprint limit values currently in place in Finland.
Australia needs to establish and implement standardised, domestically based, embodied carbon standards that are both independent and transparent. And these standards need to align with pertinent international benchmarks, such as ISO 14025 (related to environmental labels and declarations) and EN 15879 (related to terms and definitions for Life Cycle Analysis data testing or calculation).
The GBCA is leading this effort, which is a positive step toward more regenerative design and construction practices. As an industry, we can play a leading role in advancing these changes in all our projects and contribute to a more holistic approach to designing and building the world’s best places — places people, and the planet, love.
This feature first appeared as part of a masterclass for the Green Building Council of Australia (GBCA).
Images: University of Queensland Global Change Institute, Brisbane, Australia. Photography by Peter Bennetts.
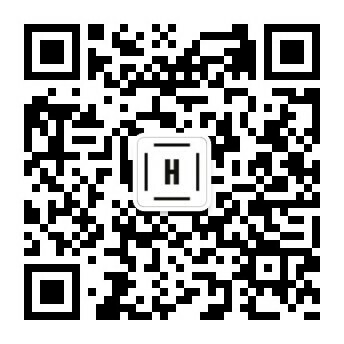
Scan this QR code with your phone to follow Hassell on WeChat.